uniserver
Well-known member
Basics for first time cap job:
http://www.radioshack.com/product/index.jsp?productId=3932529
4.5" Mini-Diagonal Cutters
Model: 6400061 | Catalog #: 64-061
$7.49
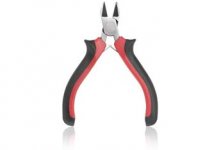
http://www.radioshack.com/family/index.jsp?categoryId=2032313&allCount=212&s=A-StorePrice-RSK&fbc=1&f=PAD%2FProduct+Type%2FSoldering+irons&fbn=Type%2FSoldering+irons&filterName=Type&filterValue=Soldering+irons
Model: 64-2051 | Catalog #: 64-2051
15-Watt Soldering Iron with Grounded Tip is an ideal choice for integrated circuit work.
Price:
$8.99
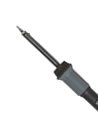
http://www.radioshack.com/product/index.jsp?productId=12582876
NTE 83-1018-0186 186-18 Rosin Liquid Flux Pen®
Model: 83-1018-0186 | Catalog #: 55047965
$8.71
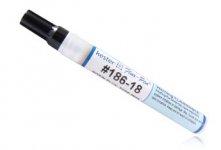
http://www.radioshack.com/product/index.jsp?productId=2062717
High-Tech Rosin Core Silver-Bearing Solder (1.5 Oz.)
Model: 64-013 | Catalog #: 64-013
$7.49
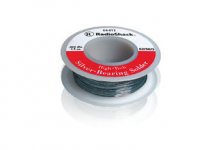
Hopefully you will not have to use this, but you should get some just incase, for bad traces.
http://www.radioshack.com/product/index.jsp?productId=2062641&retainProdsInSession=1&znt_campaign=Category_CMS&znt_source=CAT&znt_medium=RSCOM&znt_content=CT2032227
50-Ft. White Insulated Wrapping Wire (30AWG)
Model: 278-502 | Catalog #: 278-502
$5.49
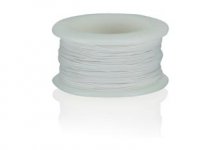
With these basics you should be able to reasonably complete a complete a cap job.
There is 3 different methods to remove old caps:
1. You can desolder them, in the wiki they talk about using 2 soldering irons one on each side of the cap to remove it.
2. You can cut the cap as close to the bottom with nippers and then pull off debris and then desolder the leads individually.
3. My favorite, Twist them off with some small electronics needle nose pliers, and just leave the (flush) portion of the lead remnants on the pads.
To install the caps:
1. Clean the pad/pad area if there is any electrolyte goo from old leaky caps, to remove pad corrosion (if any) some use standard #2 pencil eraser
2. Flow some solder into the pads
3. Flux pads
4. Place part
5. Flow each side to make a nice solid mechanical and electrical connection
done.
http://www.radioshack.com/product/index.jsp?productId=3932529
4.5" Mini-Diagonal Cutters
Model: 6400061 | Catalog #: 64-061
$7.49
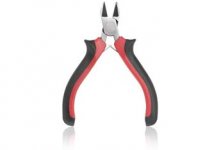
http://www.radioshack.com/family/index.jsp?categoryId=2032313&allCount=212&s=A-StorePrice-RSK&fbc=1&f=PAD%2FProduct+Type%2FSoldering+irons&fbn=Type%2FSoldering+irons&filterName=Type&filterValue=Soldering+irons
Model: 64-2051 | Catalog #: 64-2051
15-Watt Soldering Iron with Grounded Tip is an ideal choice for integrated circuit work.
Price:
$8.99
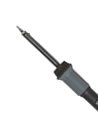
http://www.radioshack.com/product/index.jsp?productId=12582876
NTE 83-1018-0186 186-18 Rosin Liquid Flux Pen®
Model: 83-1018-0186 | Catalog #: 55047965
$8.71
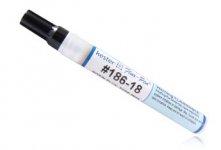
http://www.radioshack.com/product/index.jsp?productId=2062717
High-Tech Rosin Core Silver-Bearing Solder (1.5 Oz.)
Model: 64-013 | Catalog #: 64-013
$7.49
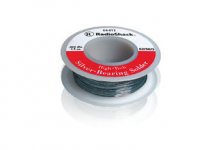
Hopefully you will not have to use this, but you should get some just incase, for bad traces.
http://www.radioshack.com/product/index.jsp?productId=2062641&retainProdsInSession=1&znt_campaign=Category_CMS&znt_source=CAT&znt_medium=RSCOM&znt_content=CT2032227
50-Ft. White Insulated Wrapping Wire (30AWG)
Model: 278-502 | Catalog #: 278-502
$5.49
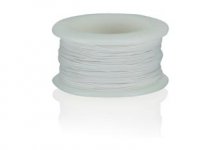
With these basics you should be able to reasonably complete a complete a cap job.
There is 3 different methods to remove old caps:
1. You can desolder them, in the wiki they talk about using 2 soldering irons one on each side of the cap to remove it.
2. You can cut the cap as close to the bottom with nippers and then pull off debris and then desolder the leads individually.
3. My favorite, Twist them off with some small electronics needle nose pliers, and just leave the (flush) portion of the lead remnants on the pads.
To install the caps:
1. Clean the pad/pad area if there is any electrolyte goo from old leaky caps, to remove pad corrosion (if any) some use standard #2 pencil eraser
2. Flow some solder into the pads
3. Flux pads
4. Place part
5. Flow each side to make a nice solid mechanical and electrical connection
done.