Crutch
Well-known member
Hi everyone, I’m new here and have found the forums to be incredibly helpful (thanks)!
I recently got my hands on an SE/30 that was supposedly recapped but I have my doubts. The caps look exactly like the originals based on photos I’ve seen, and it looks to me like there’s a bit of residue around the bases. Is there a way to tell whether these are really old, or someone just replaced them with really authentic vintage looking new caps?
By the way I started having doubts because I think the SCSI chip is bad (haven’t tried cleaning it yet - that’s next). I’ve tried connecting several known good drives to the internal SCSI and it will only see them for a few seconds, if at all, before I get random crashes. There is definitely some black crud around the SCSI chip pins.
Thanks for any thoughts!
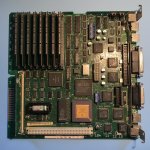
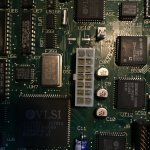
I recently got my hands on an SE/30 that was supposedly recapped but I have my doubts. The caps look exactly like the originals based on photos I’ve seen, and it looks to me like there’s a bit of residue around the bases. Is there a way to tell whether these are really old, or someone just replaced them with really authentic vintage looking new caps?
By the way I started having doubts because I think the SCSI chip is bad (haven’t tried cleaning it yet - that’s next). I’ve tried connecting several known good drives to the internal SCSI and it will only see them for a few seconds, if at all, before I get random crashes. There is definitely some black crud around the SCSI chip pins.
Thanks for any thoughts!
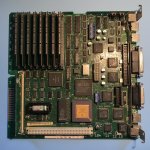
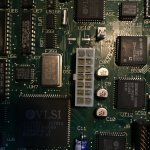
Last edited by a moderator: