Alan Gamma
Member
I need some help from someone with more soldering experience than me. I am trying to repair a Macintosh SE/30 board that was given to me in good condition (they replaced the internal battery sometime in the 90s, but the caps were leaking pretty bad). Anyway the desoldering process went pretty well except for the radial caps in C2 and C11 which were a nightmare to get out! I think it was due to the ground plane absorbing almost all the heat my soldering iron could put out, but eventually they slid out leaving solder in the hole.
After that I was replacing the SMD caps tediously but things were going well until I got to C2. I managed to get enough solder hot enough to get one end of the cap in the hole, but the other end (connected to the ground plane) would just not melt. Things I tried:
* Adding fresh solder to both sides (I’m using lead-free btw) so its almost mounding, and then heating it while pressing one leg of the cap into the hole. No luck,.
* WIping a desoldering wick across the fresh solder. This actually worked pretty well at first but it didn’t remove the solder deep in the hole.
* Getting frustrated and turning the heat up higher and higher while wiping with the wick, which ended up scratching some of the board
* Using a solder sucker to try to suck out the solder, which really did nothing (see above about how difficult it was to even get the solder to flow!)
* Holding the iron against the backside for a long time in an attempt to heat the entire ground plane, which ended up scorching the board!
I think the biggest problem here is that I ran out of patience. Due to COVID I wasn’t able to get help from my experienced friends and just kept pushing.
Anyway here’s some pictures of the damage for C2:
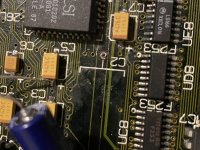
The top doesn’t look so bad although you can see I scratched the trace next to it (argh).
And the bottom:
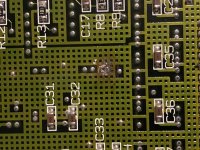
Oh my god it looks so much worse zoomed in like this
My questions:
* How screwed am I? Have I irreversably damaged the board?
* I’m using a Weller WES51 (https://www.amazon.com/gp/product/B000BRC2XU), is it possible it just can’t put out enough heat?
* How can I get the solder flowing so the leg can be put in? What temperature should I be using?
After that I was replacing the SMD caps tediously but things were going well until I got to C2. I managed to get enough solder hot enough to get one end of the cap in the hole, but the other end (connected to the ground plane) would just not melt. Things I tried:
* Adding fresh solder to both sides (I’m using lead-free btw) so its almost mounding, and then heating it while pressing one leg of the cap into the hole. No luck,.
* WIping a desoldering wick across the fresh solder. This actually worked pretty well at first but it didn’t remove the solder deep in the hole.
* Getting frustrated and turning the heat up higher and higher while wiping with the wick, which ended up scratching some of the board
* Using a solder sucker to try to suck out the solder, which really did nothing (see above about how difficult it was to even get the solder to flow!)
* Holding the iron against the backside for a long time in an attempt to heat the entire ground plane, which ended up scorching the board!
I think the biggest problem here is that I ran out of patience. Due to COVID I wasn’t able to get help from my experienced friends and just kept pushing.
Anyway here’s some pictures of the damage for C2:
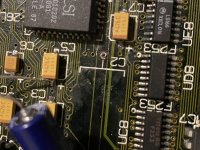
The top doesn’t look so bad although you can see I scratched the trace next to it (argh).
And the bottom:
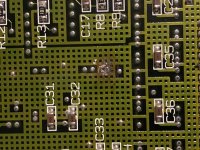
Oh my god it looks so much worse zoomed in like this
My questions:
* How screwed am I? Have I irreversably damaged the board?
* I’m using a Weller WES51 (https://www.amazon.com/gp/product/B000BRC2XU), is it possible it just can’t put out enough heat?
* How can I get the solder flowing so the leg can be put in? What temperature should I be using?