croissantking
Well-known member
I picked up an SE/30 on eBay in very good condition. It runs however there are some odd issues so I’ve been inspecting the logic board. Someone has had a go at recapping it but they have done a bodge job (it’s terrible) and even ripped some traces in the process, so I am redoing the work.
Regarding the attached image, there is a ripped trace and I assume that the repair wire (neatly installed, surprisingly) is in place for this reason. Can someone who has some knowledge of this board please advise if this repair has been done correctly?
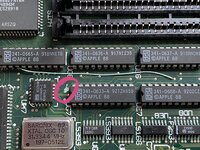
Regarding the attached image, there is a ripped trace and I assume that the repair wire (neatly installed, surprisingly) is in place for this reason. Can someone who has some knowledge of this board please advise if this repair has been done correctly?
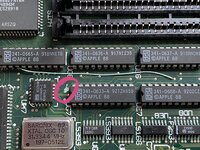
Last edited: